Tax Considerations for Remodeling or Expanding a Manufacturing Facility
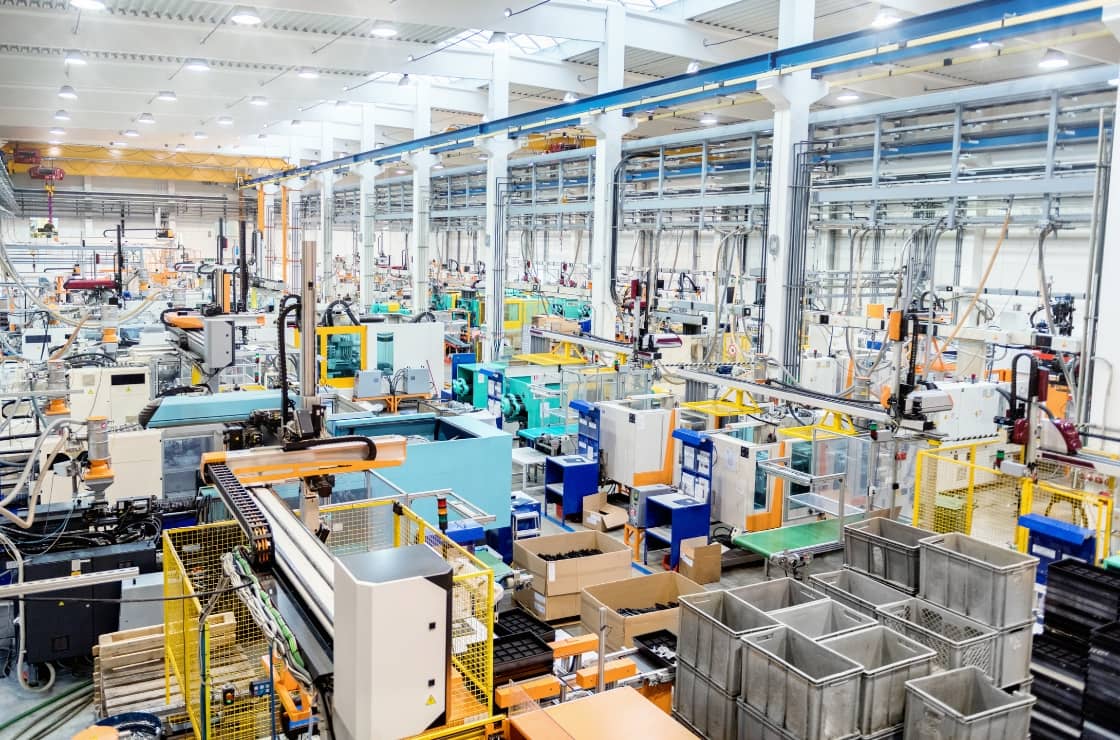
Planning to modernize or expand your manufacturing facility? The tax implications could have a bigger impact on your bottom line than you might think. Smart tax planning isn't just about compliance, it's a strategic tool that can significantly reduce your project costs and strengthen your competitive position.
Depreciation Benefits
When it comes to depreciation, timing is everything. Here's what you need to consider:
Bonus Depreciation: This is phasing out over the next few years:
- 40% in 2025
- 20% in 2026
- 0% in 2027
Bonus depreciation allows you to write off a significant portion of eligible asset costs in the year they are placed into service. Unlike Section 179, bonus depreciation can create a tax loss, making it a valuable tool for businesses with fluctuating profits.
- Section 179: This offers more flexibility, allowing you to expense up to $1.25 million in qualifying equipment purchases , with a total purchase ceiling of $3.13 million. Unlike bonus depreciation, you can cherry-pick which assets to apply this to, though it can't create a tax loss.
Cost Segregation Opportunities
A cost segregation study can uncover substantial tax savings by identifying building components eligible for accelerated depreciation. Examples include specialized electrical systems, manufacturing-specific plumbing, and HVAC systems. Additionally, these studies may classify certain expenses as repairs, enabling immediate deductions instead of long-term depreciation. Beyond immediate tax benefits, these studies provide valuable documentation for future improvements and insurance claims.
Federal Tax Credits and Benefits
Energy Efficiency Incentives
- Section 48 Investment Tax Credits: These credits reduce your tax liability for energy efficiency improvements like solar panels, geothermal systems, or energy-efficient HVAC upgrades.
- Section 179D Deduction: This incentive applies to qualifying energy-efficient building modifications such as lighting, HVAC systems, and building envelope improvements. These deductions not only lower project costs but also reduce long-term energy expenses.
Research and Development
Manufacturing upgrades often qualify for R&D credits, particularly when developing new processes or products. However, recent changes under Section 174 require capitalization of research costs, adding complexity to tax planning. Careful analysis is essential to maximize credits while complying with capitalization rules.
Opportunity Zones
If your facility is in a Qualified Opportunity Zone, you may qualify for tax deferrals or reductions on capital gains. These incentives can enhance project returns and contribute to community development goals.
Interest Expense Considerations
With rising interest rates, Section 163(j) limitations on interest expense deductions are more critical than ever. Generally, the deduction for net interest expense is capped at 30% of adjusted taxable income. For large, debt-financed projects, understanding these rules can help you plan optimal funding strategies and minimize tax exposure.
State and Local Benefits
Nebraska Incentives
The ImagiNE program offers various benefits for manufacturing investments, including:
- Wage credits
- Investment credits
- Sales tax refunds
Planning early can ensure your project meets program requirements and maximizes these benefits. Additionally, property tax relief and Tax Increment Financing (TIF) programs can significantly reduce costs for projects in designated development zones.
Sales Tax Considerations
Many manufacturing-related improvements qualify for sales tax exemptions or reductions. This applies to equipment, building materials, and construction costs. Proper documentation and purchasing procedures are critical to capturing these benefits.
As you plan your manufacturing facility improvements, remember that timing is crucial for maximizing tax benefits. With bonus depreciation phasing out and interest rates affecting financing decisions, early planning is key. Consider conducting a cost segregation study at the project's outset, and don't overlook energy efficiency incentives that can provide both immediate tax savings and long-term operational benefits. Additionally, Nebraska's state-specific programs, like ImagiNE, can significantly enhance your project's financial outlook through various credits and exemptions.
Maximize Your Facility Investment with Lutz
Tax regulations are constantly evolving, making it crucial to work with advisors who understand both manufacturing and tax strategy. At Lutz, our team of manufacturing industry specialists knows how to help clients navigate these complexities while maximizing available benefits. Contact us to explore how our expertise can support your facility improvement plans.
June 2, 2025 Update: Proposed changes under the “One, Big, Beautiful Bill” may impact some of the information below, including bonus depreciation, Section 179 limits, and R&D expensing. We are actively monitoring the legislation and will update this content if and when the bill is signed into law.
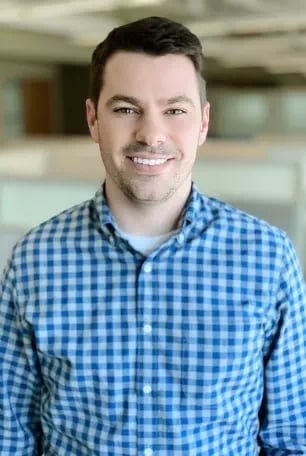
- Analytical, Achiever, Futuristic, Responsibility, Maximizer
Adam Austin
Adam Austin, Tax Shareholder, began his career in 2009. He has developed comprehensive expertise in tax consulting and compliance through his years of public accounting. Adam also actively contributes to the firm's growth through his involvement in recruiting initiatives.
Focusing on tax services for privately-held businesses, Adam serves clients across the healthcare, manufacturing, agriculture, and real estate industries. He oversees internal projects while providing deliberate compliance solutions.
At Lutz, Adam leverages his analytical mindset and futuristic outlook to make the complex simple for clients. His ability to anticipate potential implications enables him to create plans that position clients for long-term success, making him a trusted advisor and a valued strategic resource across the firm.
Adam lives in Omaha, NE, with his wife Ashley and their three children, Emilia (Millie), Charlie, and Will. Outside the office, he can be found cheering on Husker football, hunting, fishing, and hiking with his family.
Recent News & Insights
Are all-time highs a sell signal?
What To Know About the 2026 Interoperability & Prior Authorization Rule
Defining HR Roles
Accrual or Cash Basis for Income Tax: Why It Matters More Than You Think
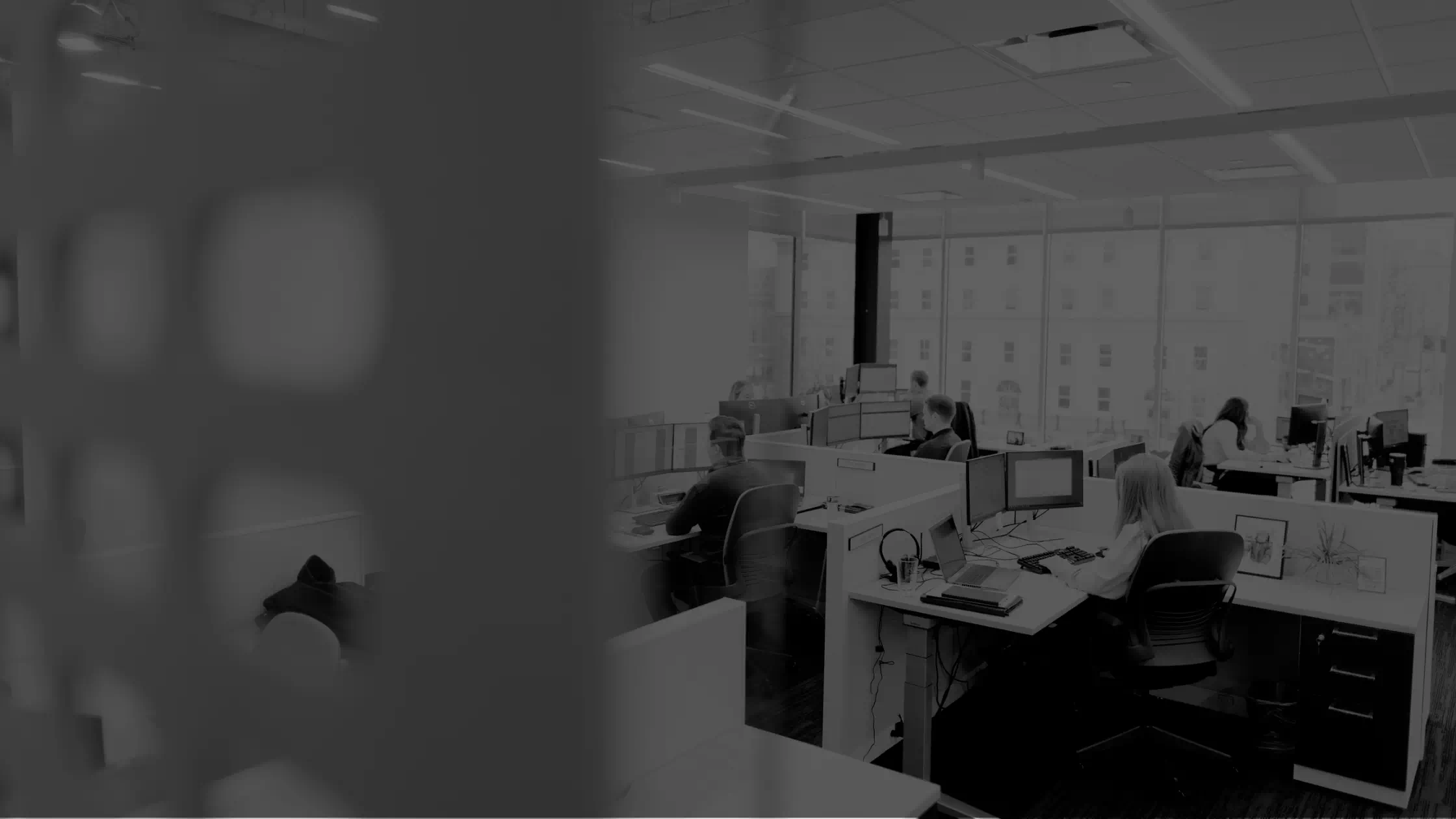
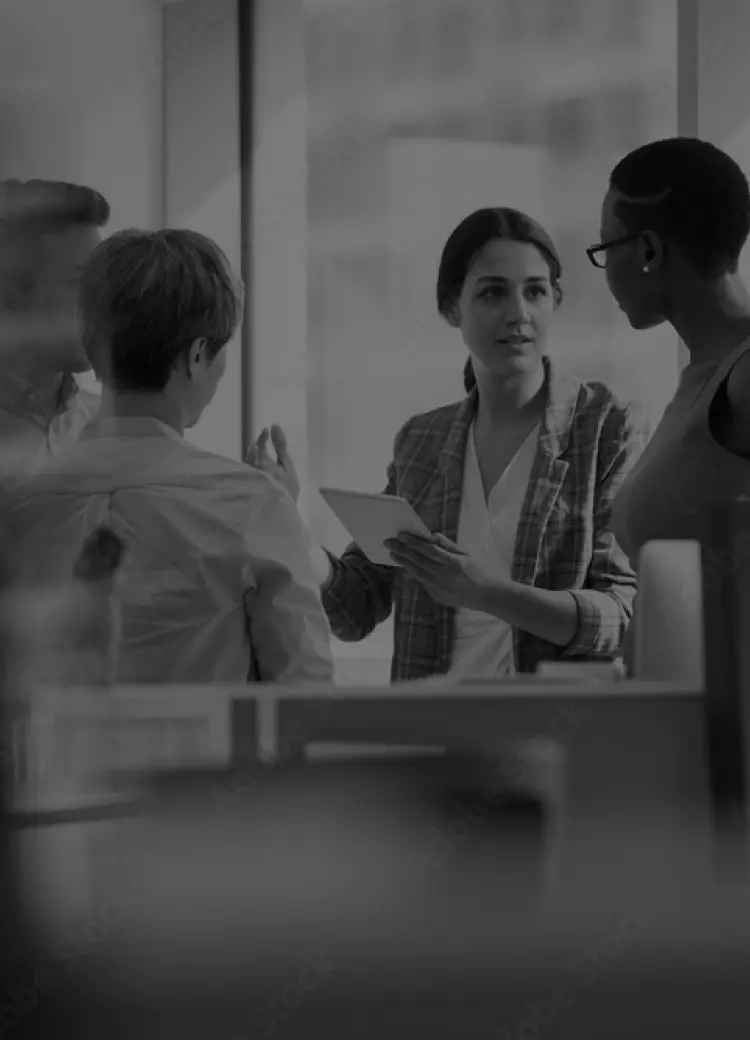